Closing the circle
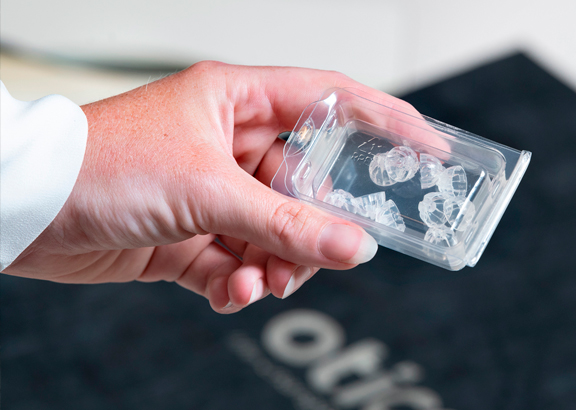
We recognise the critical importance of the transition towards a circular economy to minimise the environmental impact, resource consumption and waste generation and to maximise resource efficiency.
Our actions in this area span from resource efficiency and the use of secondary raw materials to value retention and responsible end-of-life management.
Testing, Sharing, Caring
We have developed a special test hearing aid that can be used by multiple individuals over a trial period. After each trial, it is returned to us, thoroughly cleaned and prepared for the next user.
Rethinking packaging
Is it possible to reduce the carbon footprint of each charger packaging of our hearing aids’ unit by 80%? Yes, it is. We have launched a new plastic-free charger packaging across our four hearing aid brands worldwide. Our Diagnostic business area has incorporated recycled materials into its packaging, using recycled polyethylene plastic in the plastic bags and cardboard containing up to 98% of recycled materials.
More innovation, less plastic
Each of our hearing aids comes with a small plastic container for storing replaceable filters that keep earwax out of the device. These filters need to be changed often, so we have redesigned the container to use less plastic. By improving the moulding process and redesigning the container, we have cut plastic use by 53% per unit.
Prolonging lifespan
We perform numerous repairs to ensure our users’ hearing aids stay in great condition and extend their lifespan. Maintenance and repair services are available for all hearing aid models and brands for up to five years after they are discontinued. For our diagnostic devices, we offer maintenance services to our customers to ensure that normal wear and tear does not affect their usability or quality. We also provide worldwide repair service if required.
Onboarding new materials
We have introduced a new material for the inlets inside our hearing aids, eliminating the use PFAS in this component. This change makes our inlets easier to recycle. We continuously work towards eliminating these chemicals without compromising the quality and safety of our devices. Additionally, we have been using recycled plastic in our diagnostics devices since 2014 in collaboration with our largest supplier. This material comes from waste generated during our supplier’s internal plastic production.